Petrochemical Pumps for Plastics Manufacturing
Pumps play an essential role in the chemical plastics industry.
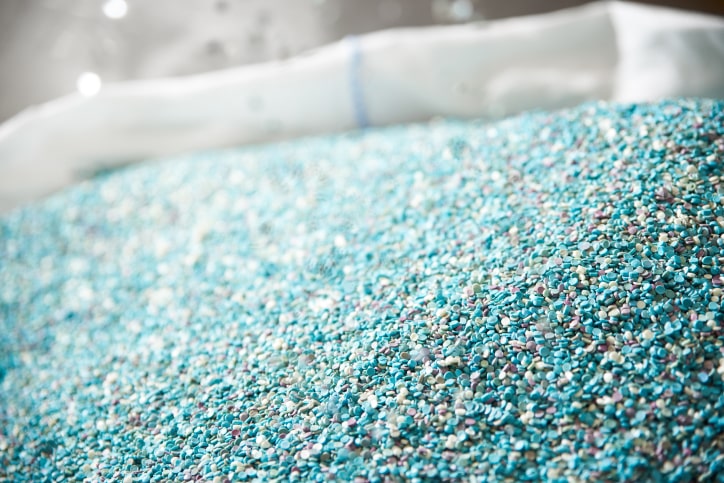
The chemical production of plastic is a very complex process that requires a wide range of skills and knowledge. Some of the most important steps in plastics manufacturing include feeding, processing, molding, and finishing.
What role do pumps play in the chemical plastics industry?
pumps play an important role in the chemical plastics industry. They make a significant contribution to ensuring that materials and liquids during manufacturing process can be transported. Pumps ensure that materials are directed to the right location and ensure that chemical reactions run efficiently. Pumps are therefore an indispensable part of the chemical plastics industry.
Petrochemical pumps for plastics manufacturing require careful design. It should be ensured that the pumps are working correctly and are not causing leaks. They must be designed to last a long time. In addition, the flow rate must not decrease under extreme conditions. To ensure that the pump technology is working properly, the pumps must be serviced regularly. Even the seals must be renewed at regular intervals. The pumps must be correctly sized for safety and reliability. They should be configured to use the requisitions match the process and environment.
Pumps for plastic manufacturing
In this branch of industry, the positive displacement pumps. This type of pump is particularly impressive due to its high efficiency and low maintenance costs. They are easy to install and can be used in many different applications. Displacement pumps are often found in chemical industry usage. They are convincing when pumping liquids of higher viscosities. But even in the event that a pumping medium contains solid particles such as those found in plastic and Plastics manufacturing That is the case, they provide a reliable pumping process. In addition, most positive displacement pumps are easy to handle due to their compact size and quiet operation. They can also be used in many different operating environments.
The positive displacement pumps also include our wobble ring pump. Die wobble ring pump has all the features to meet the requirements of plastic manufacturing. It is powerful, reliable and easy to use. In addition, it can also be used in difficult environments. Because it has a robust design and a long lifespan. It also ensures a constant pressure and flow rate, so you always get consistent quality. This ensures that your requirements are met and that you can expect maximum reliability.
Feel free to see for yourself and browse through our product brochure.
After individual advice, you have the option of renting or buying your wobbling ring pump model tailored to your needs at short notice.
What are the three types of plastics?
There are thermoplastics, elastomeric plastics and duroplastics.
thermoplastics are very malleable and can be deformed by heating to a specific temperature. They can then be shaped into the desired shape. They are lightweight, robust and cost-effective and are therefore particularly suitable for industrial mass production.
thermosetting plastics are hardened by introducing fillers, such as glass fibers, into the polymer matrix. As a result, they are both malleable and flexible. They are also extremely stable and resistant to high temperatures, acids and solvents.
elastomer plastics On the other hand, they are very flexible and can be stretched and compressed in various forms. They are also able to regain their original shape after deformation. For this reason, elastomer plastics are often used in areas where high elasticity and good recoverability are required. They are also used in many medical applications, such as in the manufacture of implants and hip replacement parts.
What does petroleum have to do with plastic production?
In the petrochemicals is crude oil or natural gas processed into a wide variety of basic chemical substances. Volatile carbon compounds are the most common. This also includes the substances from which plastics are later made.
The substances from which plastics are later manufactured are mainly hydrocarbons, carbon compounds such as polymers, polyols and additives. These substances are combined under various conditions, such as pressure, heat and chemical reactions, to produce different types of plastics.
These raw materials are then converted into more complex ones through further chemical reactions molecules further processed. Various plastics can also be produced in this way. These are used, for example, in automotive engineering, in electrical engineering, for food packaging or used in medical technology.
The feedstock For plastic production, oil or coal is usually used. However, the raw material can also be obtained from waste products, sugar cane, corn, wood or plant fibers, such as cotton. In addition, there are also plastics that are made from biodegradable materials, such as polylactic acid (PLA).
These biodegradable plastics are a sustainable alternative to conventional plastics. Similar to these, they can be used in many different industries. These include the areas of agriculture, transportation, the packaging industry and even medicine. They are non-toxic, durable, easy to process and have a low impact on the environment. However, due to their high costs, they are not yet widely used and are not an alternative worth mentioning at the moment.
What are the steps involved in plastic production?
The manufacturing process is divided into supply, processing, shaping and finishing.
When supplied, the feedstocks, which are required to produce the plastic, is fed into the production plant.
The raw materials are then mixed and processed in one processing step using special machines until they reach the desired consistency.
The mass is then shaped by a special machine in a forming step to obtain the final shape of the product. Then, the surface of the finished product is polished to achieve a glossy finish.
The surface of the finished product is then processed using a special polishing machine to obtain a smooth and shiny surface if necessary.
Last but not least, the product is cleaned so that it is flawless and the final quality is achieved.
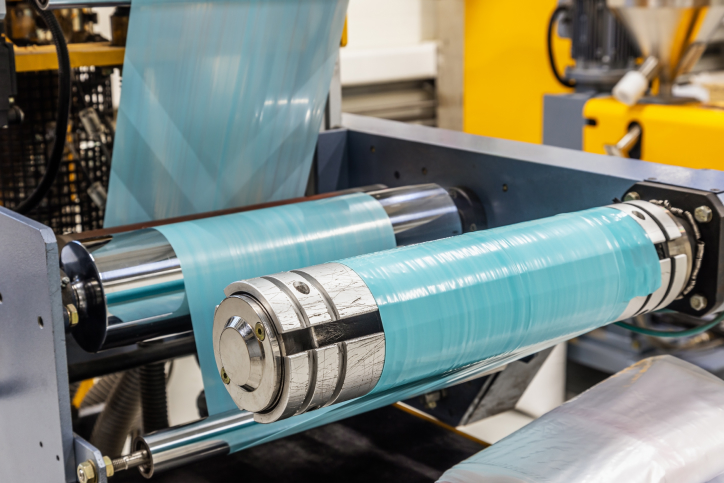
How much crude oil is needed for 1kg of plastic?
It depends on what type of plastic is being used. As a rule, 1 kg of plastic requires approximately 1.5 to 2.5 kg crude oil needed.
It is important to carefully select plastics that can be produced more efficiently and require less crude oil. Recyclable plastics are a good choice. They can be reused several times and thus reduce the amount of crude oil required for production. Biodegradable plastics are also suitable, as they are used in environmental can be returned. And without having any harmful effects on the environment.