Pumps for industrial adhesive production
Pumps play a key role in industrial adhesive production.
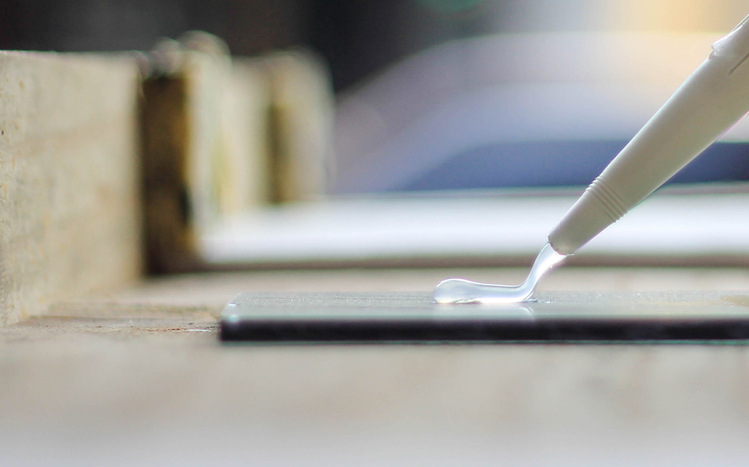
pumps for the production of industrial glues are one of the most important components in many industrial processes. They are able to move large quantities of liquids and fluids. In addition, they can also individual particulates suspend in a liquid. This makes them an important component in adhesive production to ensure that the right amount of liquid is used for the process.
What are adhesives?
glues are substances that connect two or more objects together and hold them firmly together. They are generally made from organic or inorganic materials, such as polymers, resins or paste. They are sold in various forms, such as liquids, pastes, sprays, or films. Most adhesives are inorganic polymers, which are produced through so-called polymerization. They are heat resistant, as well as resistant to chemicals and also wear-resistant. They are therefore suitable for use in various industries, for example for bonding metal parts in the automotive industry.
What is the role of pumps in the production of industrial adhesives?
Pumps play an important role in the production of industrial adhesives. They are essential for dosing and distributing the various components in the manufacturing process. They can also be used to printing to increase the mixture and thus achieve the desired consistency.
pump types There are various sizes and configurations for the production and transportation of industrial adhesives. This ensures that they meet the needs of the process. They are also equipped with various types of motors to achieve the required performance for the respective process.
Die pump housing are made from various materials, which are tailored to the respective purpose. There are pump housings made of plastic, metal or stainless steel. In addition, many pumps are able to handle both cold and hot adhesives. They are also equipped with a range of safety features to ensure that they function correctly.
Pumps for industrial adhesive production
Our wobble ring pump is well suited for adhesives. It is easy to operate and works reliably. It is also very robust and its pump output does not subside even in difficult environments. It also has a long lifespan so that it can be used for many years.
In addition, the wobble ring pump requires very little maintenance and can be easily cleaned. It is also available with a variety of connectors so that it can be used for various applications. It is available for rent or at low cost and requires no special maintenance. This makes it a very reliable solution for many applications, including especially for conveying adhesives.
You can find more information about the wobble ring pump in our product brochures.
You have the option to flexibly rent or, of course, buy your ideal wobble ring pump version at short notice. We are happy to help you find a pump that is tailored to your needs.
What kind of adhesives are there?
There are various types of adhesives that are used for various purposes. This includes conventional Adhesives such as wood glue, styrofoam glue, acrylic glue, silicone glue, and polyurethane adhesives. These species can be found in many homes and offices.
In addition, there are special adhesives for industrial Use, such as hotmelt adhesives, cyanoacrylate adhesives, epoxy resins, polyimide adhesives, polysulfide adhesives and UV adhesives. Hotmelt adhesives are adhesives which melt at temperatures between 130°C and 160°C and then harden. Cyanoacrylate adhesives are extremely fast-curing adhesives that harden when in contact with moisture. They are also known as superglue. Epoxy resins are chemically resistant adhesives that consist of two components and harden at room temperature. Polyimide adhesives are highly heat-resistant and high-temperature resistant. Polysulfide adhesives are solvent-based adhesives that harden at room temperature. UV adhesives are adhesives that harden when exposed to UV light.
These adhesives are used in many industrial applications because they enable plastics processing that is faster, lighter and more cost-effective. They offer a range of benefits, including quick and easy application, a high strength, ruggedness and excellent environmental resistance.
How is adhesive made?
Adhesive is usually made from a mixture of organic solvents, resins, and polymers. This mixture is then heated to a specific temperature. As a result, the adhesive connection activates and thus gives the adhesive strength. The adhesive is then filled into a suitable container to pack and transport.
There are more than 250,000 different adhesive formulations worldwide. The requirements vary greatly and therefore the material composition. The modification of base substances and addition of additives can be used here to meet the wide range of applications.
During production, a distinction is generally made between adhesives based on natural or synthetic raw materials. A combination is also possible here.
Natural adhesives can be made from protein, vegetable oils or resins. synthetic adhesive connections On the other hand, they are based on acrylates, polyurethanes or silicone. Depending on requirements, further additives such as fillers, crosslinkers or plasticizers can then be added to achieve the desired properties.
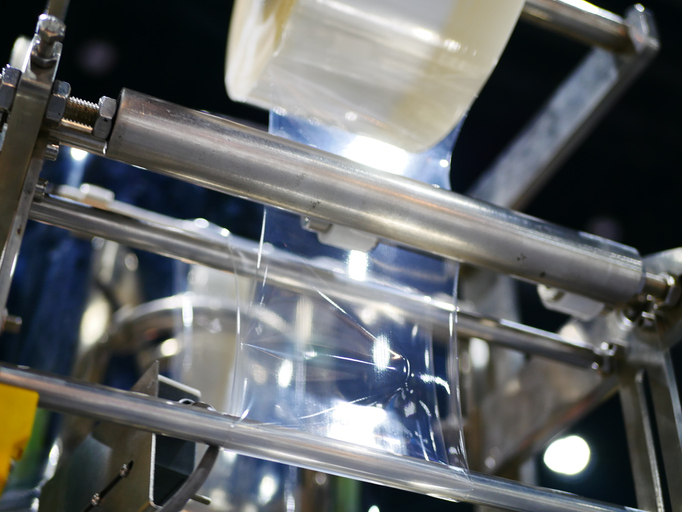
What causes the adhesives to stick?
Adhesives stick together through a chemical reaction in which molecules are exchanged between two surfaces. These molecules then form a kind of network that connects the surfaces and thus creates a strong bond.
This strong bond is very durable and can also be released again if necessary. This is most commonly achieved by chemical solvents, which remove the molecules of Bonding Break open and thus break the bond again.
Within which industrial sectors are adhesives used most frequently?
Adhesives are most commonly used in the automotive industry, the electronics industry, the wood industry, the aircraft industry and the packaging industry.
In addition, certain special adhesives also used in other industrial sectors such as medical technology, the construction industry, the furniture industry, the glass industry and the textile industry. The use of adhesives is very widespread in industry. However, they are also regularly used at home or while pursuing hobbies.
Are all adhesives toxic and harmful to the environment?
Adhesives can be of varying degrees of toxicity. It depends on which adhesive is used. Some are highly toxic, others are harmless.
It is important to find out about the ingredients in the adhesive and to check whether there is an adverse effect on health. In addition, the adhesive should only be carried out in accordance with the instructions for use and in compliance with all Hazardous substance labels be applied.
The manufacturing process Adhesives can actually be harmful to the environment. This is caused by the many chemical compounds it contains, which can be toxic and harmful to the environment under some circumstances. Many of these chemical compounds are used in the production of adhesives and can lead to air pollution and poor water quality. In addition, these compounds can be harmful to groundwater when the product is broken down. Environmentalists therefore recommend the use of biodegradable adhesives as they emit fewer pollutants into the environment.