Industrial pumps for conveying and processing silicones
Pumping silicones requires industrial pumps that are able to efficiently handle the viscous consistency of this substance.
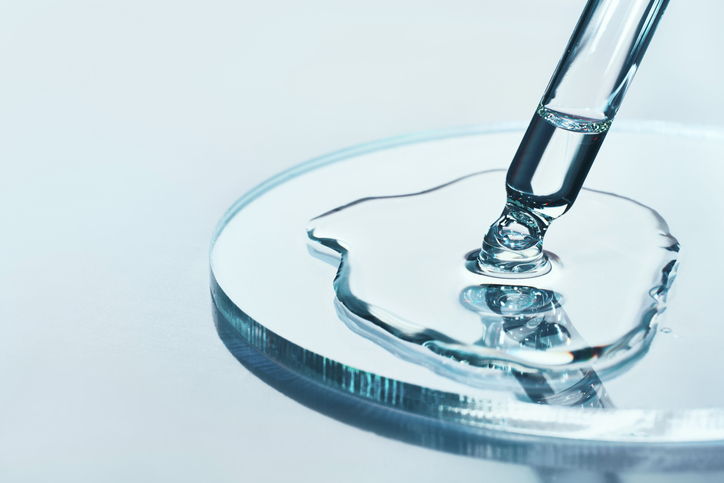
industrial pumps Are an essential part of the extraction and processing of silicones. These special pumps are used in various industries, including chemistry-, groceries- and cosmetics industry.
Pumping silicones requires industrial pumps that are able to viscose Managing the consistency of this substance efficiently. Silicones are silicone-based polymers that are often called Lubricants, Sealants Or coatings are used. They can occur in various forms, such as liquids, pastes, or gels.
Selecting the right pump technology for conveying and processing silicones depends on various factors. This includes the viscosity of the silicones, the required Conveying capacity, the pressure that Temperature And the type of Application.
Zu unseren Industriepumpen für Silikone
The Wobble Ring Pump for Pumping Silicones
Especially pumpsystems Wobble ring pump Has proven to be one of the most efficient & reliable pump types among industrial pumps Proven for pumping silicones.
The wobble ring pump is characterized by its high dosing accuracy and its ability to easily transport even viscous media such as silicones. Thanks to its special design and the use of high-quality materials, it ensures a consistent Quality of the promoted silicones. At the same time, wear and maintenance requirements are kept to a minimum.
In addition, the wobble ring pump enables precise control of flow and pressure conditions, which ensures efficient processing of silicones. It can be used in both continuous and discontinuous processes and is suitable for a wide range of applications. This includes, for example, the production of sealants, adhesives, coatings and many other products.
The Reliability and Durability of the Wobble Ring Pump Allows Silicone Manufacturers to Production processes to make it more efficient and cost-effective. It minimizes downtime and ensures continuous production without interruptions.
We also provide a solution tailored to your needs rent The Wobble Ring Pump Our experienced technicians are available to install and set up the pump according to your requirements. We also offer regular maintenance- and inspection services to ensure that the pump is always working optimally
With our wobbling ring pump, you can benefit from the advantages of efficient and reliable silicone conveying. Contact Contact us today to learn more about our Rental options And find out the benefits of a wobble ring pump for your requirements. We look forward to working with you at optimization to help your production processes.
What role do other industrial pumps play in the production and processing of silicones
The production and processing of silicones requires precise and reliable pumps to maintain a consistent Quality and Efficiency to ensure.
The production of silicones involves various process steps in which the pumps play an important role. From the dosing From starting materials to mixing and homogenization to filling & packaging — industrial pumps are essential at every step.
From gear pumps to eccentric screw pumps to diaphragm pumps - There is a suitable solution for every application.
This Pump types Enable precise dosing, efficient mixing and homogenization of silicones as well as controlled filling and packaging.
Gear pumps Are ideal for dosing silicone oils and resins, for example. They ensure an accurate and constant flow rate, which produces results in a consistent quality of the silicones.
eccentric screw pumps On the other hand, they are ideal for conveying viscous silicone pastes. Thanks to their special construction, they can also handle abrasive or fibrous components, which can occur in some silicone compounds.
diaphragm pumps Are often used for filling silicones into containers or packaging. They enable precise dosing and at the same time prevent contamination or contamination of the silicone during the filling process.
In addition, industrial pumps also play an important role in recovery and recycling of silicone waste. By using special pumps, silicone residues can be efficiently extracted and reused, which contributes to sustainable production.
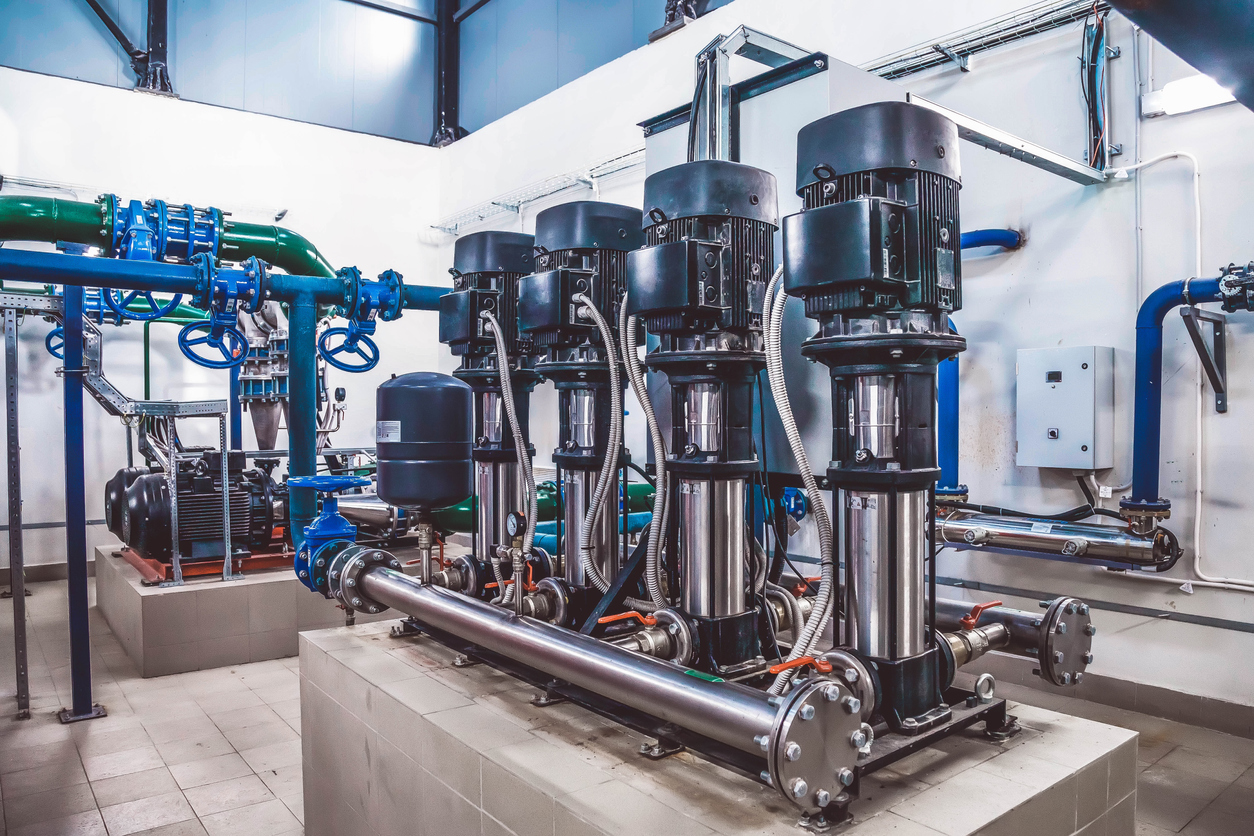
Where does silicone come from?
Silicones are organic compounds that consist of silicon, oxygen, carbon, and hydrogen. Die structure and Properties Silicones may vary depending on their chemical composition. They can be liquid or solid and have a smooth, non-sticky texture.
The history of silicones begins in the early 19th century, when the German chemist Friedrich Wöhler for the first time Silicon compounds synthesized. In the following decades, further progress was made in silicone chemistry, particularly by German scientists such as Richard Müller and Hermann Staudinger.
Silicones were initially used in Electrical engineering, as they have good insulation properties. In the 1940s, German companies such as Wacker Chemie and Dow Corning began commercial production of silicones. Since then, the areas of application of silicones have expanded significantly.
One reason for the popularity of silicones is that they are particularly sturdy Are. In addition, they are heat-resistant, cold-resistant and resistant to UV radiation and chemicals. That makes her a innovation for use in extreme environments.
However, despite their wide range of applications and benefits, there are also concerns about Environmental Impacts of silicones. Some studies suggest that certain silicones accumulated in the environment may be potentially harmful to aquatic life.
The research and unfolding of more environmentally friendly Alternatives to silicones are therefore a current topic in the chemical industry. German companies and research institutions play an important role in this and are working to find more sustainable solutions.
What are the chemical properties of silicones?
silicones Are a group of compounds that consist of silicon, oxygen, carbon, and hydrogen. They are characterized by their unique chemical properties.
One of the most remarkable properties of silicones is their high thermal stability. They can withstand extreme temperatures, both high and low. This makes them ideal materials for applications in Industry, such as in electronics or in the automotive industry.
Silicones are also hydrophobic, which means they are water repellent. This property makes them particularly useful in the production of water-repellent coatings and seals. Silicones can also be used as Lubricants Are used because they offer excellent lubricity due to their low frictional properties.
Another important aspect of the chemical properties of silicones is their chemical inertness. This means that they only react very slowly with other substances, which makes them extremely stable and enduring Acts against many chemicals. This makes them a preferred choice for medical applications, such as in implants or medical devices.
It is important to note that not all silicones are the same. There are different types of silicones with different properties and effects.
For example, there are silicone fluids, silicone greases, fluorosilicones, silicone resin, silicone rubber, and silicone elastomers.
Any type of silicone Has specific applications and benefits.
silicone fluids Are thin and have a low viscosity. They are often used in the cosmetics industry to improve products such as skincare products, hair care products, and makeup.
silicone greases On the other hand, they have a thicker consistency and are often used as lubricants in mechanical devices. They offer high temperature resistance and are water-repellent.
fluorosilicones Are characterized by their chemical resistance and their ability to function in extreme environments. They are often used in the electronics industry, for example in high-performance cables and seals.
Silicone resins are solid materials with high strength and hardness. They are used in the construction industry to seal and protect surfaces.
Silicone rubber and silicone elastomers are elastic materials that are widely used in the medical and food industries. They are used for making medical devices, seals, tubes, and food containers.