Application and function of pumps in the food industry
The requirements for pumps in the food industry are wide-ranging.
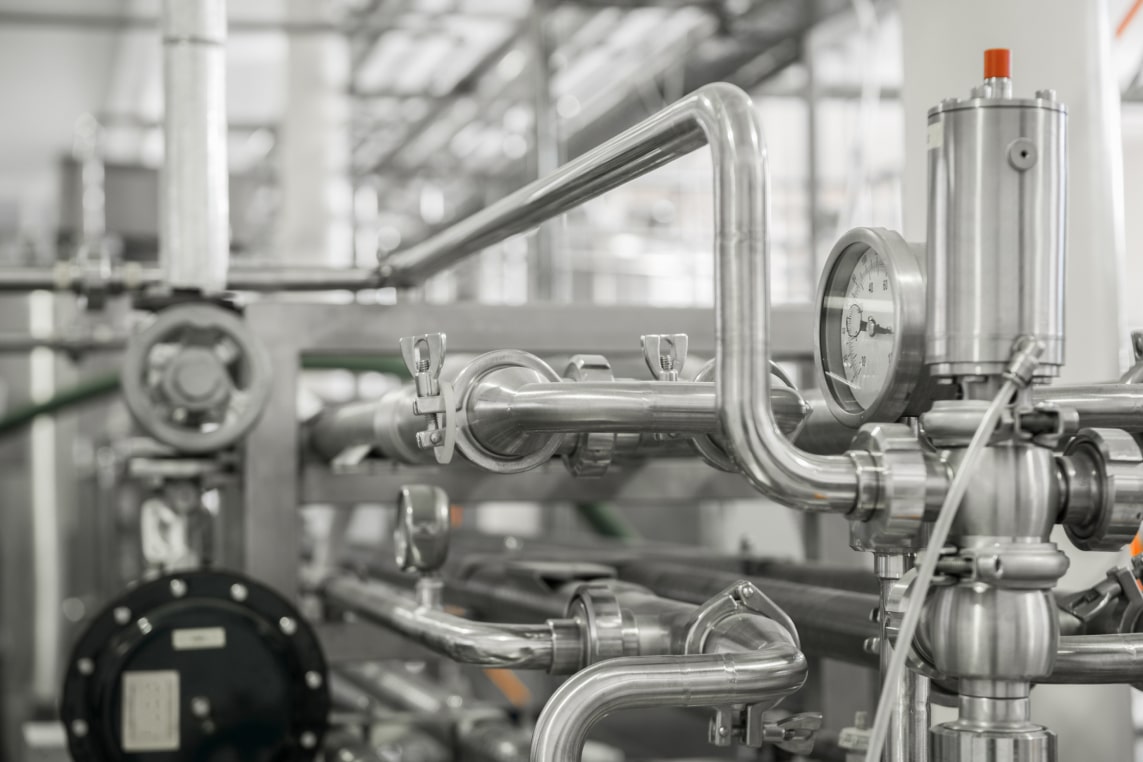
food pumps are an essential part of food industry . They are used for the production, packaging and storage of Groceries essential. The food pumps are available in various sizes and designs to meet the different needs of the food industry.
The choices when choosing the right pump per drinks or food is huge. It is important to note that food can often be transported from one station to the next. Closed systems enable hygiene and food safety.
In the food industry, liquids or pasty or does not promote flowing media at all.
What belongs to the food industry?
Die food industry is one of Germany's most important industrial sectors. Small and medium-sized companies predominate. Around 614,000 people are employed across Germany. Germany food grade is in demand internationally, which makes us the third largest food exporter in the world. Meat industry foodstuffs, finished products and confectionery are exported, as well as dairy products.
About our pumps for the food industry
What are industrial foods?
Industrial foods are foods that have been processed industrially. This includes baking, freezing or drying, for example.
Industrially produced foods have a very bad reputation, but they are not always fundamentally unhealthy. The industrial sector But always brings a certain environmental pollution with yourself.
It is divided into four stages. The first stage includes unprocessed plant parts. This includes, for example, fruit, vegetables, rice, milk, eggs, coffee or water. The main part of the diet is recommended from foodstuffs build the first stage. Second-level foods include vegetable oils or salt. Their nutritional density is lower than that of first-level foods. Third-level foods have an even lower nutritional density. Examples include bread or cheese. It is important to maintain a balance and to consume consciously in moderation. Level four foods are highly processed . This includes ready meals, soft drinks or sweets. They contain many additives and few nutrients.
Highly processed foods pose a risk to our climate due to their many industrial processes. As a result, there is still a lot of industrial energy from fossil fuels is extracted, many CO2 emissions are released into the atmosphere.
What problems does the food industry pose?
The food industry is responsible for around 45% of pollutant emissions. Not only is that a problem, but also packaging waste and food waste . These are also created during production. Every year, around 1.6 million tons end up in the trash when the food is processed.
Our wobble ring pump counteracts this, it is special energy efficient and resource-saving .
It is particularly easy to handle, maintain and clean.
Feel free to see for yourself. In our product brochure, you will find answers to all your questions.
Which pumps are used in the food industry?
food pumps must fulfill many purposes. Many foodstuffs have to be pumped several times through various pumping systems. It shouldn't matter whether that pumping medium is pasty or not flowing in liquid form. For hygienic purposes, it is important that the type of pump has a closed system.
It is quite possible that, for example, a frozen substance, i.e. at temperatures below zero degrees Celsius, must be transported. Just like a substance at 150 degrees Celsius, such as a sugar mass .
Even if the supposedly ideal pump has been found, it is also important not to ignore a number of other factors. These would be wear and tear on the one hand, and hassle-free cleaning on the other hand. The following applies here are surface roughness Below a scale of 0.8 µm, these are well suited. You can tell whether a pump can work hygienically by looking at a EHEDG certification or a 3A approval.
There are a few features that apply to Pump selection are decisive. Starting with the flow rate. The flow rate shows how much of the medium can be pumped within any period of time. Pumps should be operated at 30 to 60 percent of their maximum capacity . If the pump is too small, it can fail or run too hard. In turn, when the pump is too large, it leads to an increase in operating and acquisition costs.
An equally important factor is the nature of the material. This is based on factors such as viscosity , shear, abrasion and particle size watched.
The more viscous the pumping medium is, the more the flow rate is reduced. With this knowledge, action can be taken accordingly. Pumps are normally standardized for a maximum flow rate of 1 centipoise (cP) for water. As a result of groceries A higher viscosity Have decreases the output accordingly.
Media higher viscosity It is best to promote wobble ring pumps , diaphragm pumps, piston pumps or even rotary lobe pumps.
It is best to convey media of lower viscosity with, for example centrifugal pumps .
High viscosity also requires strong suction. Electrical and pneumatic diaphragm pumps and peristaltic pumps can produce this strong suction.
Are there pieces or particulates In the pumping medium that must not be squeezed, it is just as important to choose an appropriate pump. If you do not do this, it can damage the medium. Pumps with a high flow rate, such as wobble ring pumps , diaphragm pumps with flap check valves, or also peristaltic pumps .
At best, some foods should not be exposed to shearing. This includes, for example, meat or poultry, tomatoes or even pies. shear includes the effect of force on the pumped medium. membrane and sinusoidal pumps or wobble ring pumps are just right for that. They are gentle on materials and still produce the required suction
If materials with an increased sugar content are pumped, this leads to increased material abrasion. The one in rotary lobe pumps The special materials and coatings used counteract this. But these types of pumps in turn have problems with rotor clotting or leaking rotary seals. Once again, the best solution to the problem is diaphragm pump or the wobble ring pump.
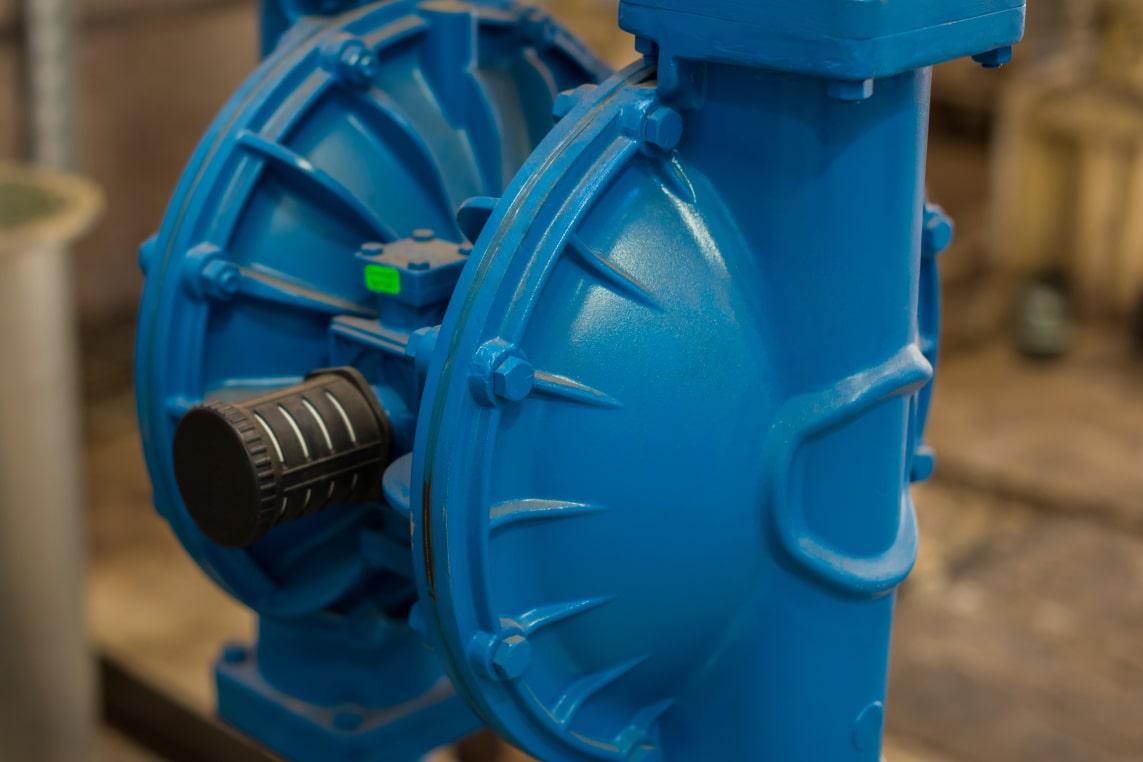
Of great importance is also the chemical Compatibility of the material of pump and the medium. Elastomer seals often lead to compatibility problems. Their shelf life is drastically reduced as soon as they come into contact with animal oil and grease is coming.
It is not only the compatibility of the transported media that plays a role, but also the compatibility with the cleaning agents. Because there are high hygiene and cleaning standards, the cleaning agents are not always well tolerated.
If all these factors have been taken into account, additional permits are required. There are uniform standards in the food industry, which must be met. The most famous is the United States Food and Drug Administration ( FDA ). food manufacturer In Europe, according to the European Framework Regulation (EC) 1935 produce. Broadly speaking, both monitor and ensure the quality of the food produced.
Would you like to learn more about pumps and their various functions and applications?
In our next article Find out how chemical pumps are used and which are best suited for the chemical industry.