Pump connection types
This article takes a closer look at the different connection types of industrial pumps.
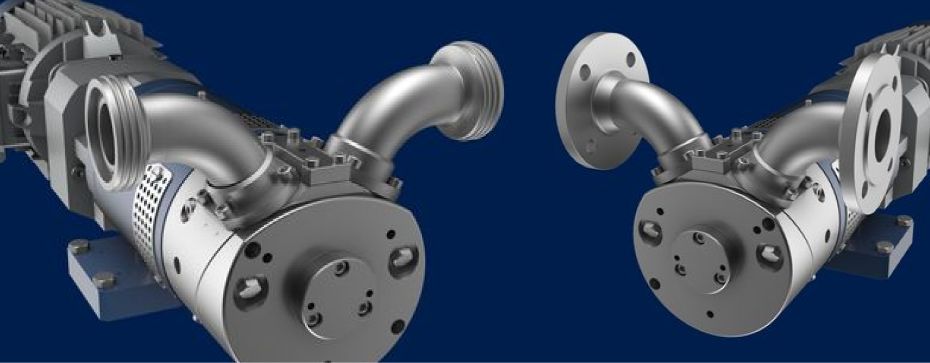
A pump is a device that is used to transport liquids or gases from one location to another. To make this possible, a pump requires various Connection typesto be connected to the appropriate pipes or hoses. This article presents the most common types of pump connections.
Die wobble ring pump is available in various designs and sizes. She is characterized by her power and reliability off. The pump can be used for both liquids and gases and is therefore suitable for a wide range of applications.
About our industrial pumps
One of the most common connection types for our wobble ring pump is the flange connection. Here, the pump is attached to the corresponding pipes or hoses using flanges. Flanges provide a stable and secure connection that can also withstand high pressures.
Another type of connection is the threaded connection. Here, the pump is attached to the pipes or hoses with threaded connections. Threaded connections are easy to install and provide a good seal.
Another alternative connection type is the Clamp closure. Here, the pump is attached to the pipes or hoses using clamps. Clamp fasteners offer quick and easy installation, but are sometimes not suitable for high pressures.
In addition to these common connection types, there are also more specific connection variants, such as the hose connection or the pipe connection. These connection types are selected depending on the area of application and specific requirements.
It is important to select the correct connection type for each pump to ensure a safe and efficient connection. When choosing the type of connection, factors such as pressure, temperature, and medium should be considered.
Overall, our wobble ring pump offers a variety of connection options to meet the individual needs of our customers. We're here to help you choose the right connection type for your application.
Feel free to take a look at our product brochures.
Which industrial pump is used for which application?
Industrial pumps are generally divided into two types of pumps: centrifugal pumps and positive displacement pumps.
Centrifugal pumps are primarily used to transport liquids. They are characterized by their high flow rate and impressive delivery height. Yet they develop their optimal efficiency only within a specific flow range. centrifugal pumps are used in various areas such as water supply, waste water treatment, the chemical industry and the food industry.
Displacement pumps, on the other hand, are suitable for transporting viscous or abrasive media. They work according to the principle of volume displacement and can therefore also transport solids. Displacement pumps are used, for example, in the oil and gas industry, the pharmaceutical industry and the paper industry.
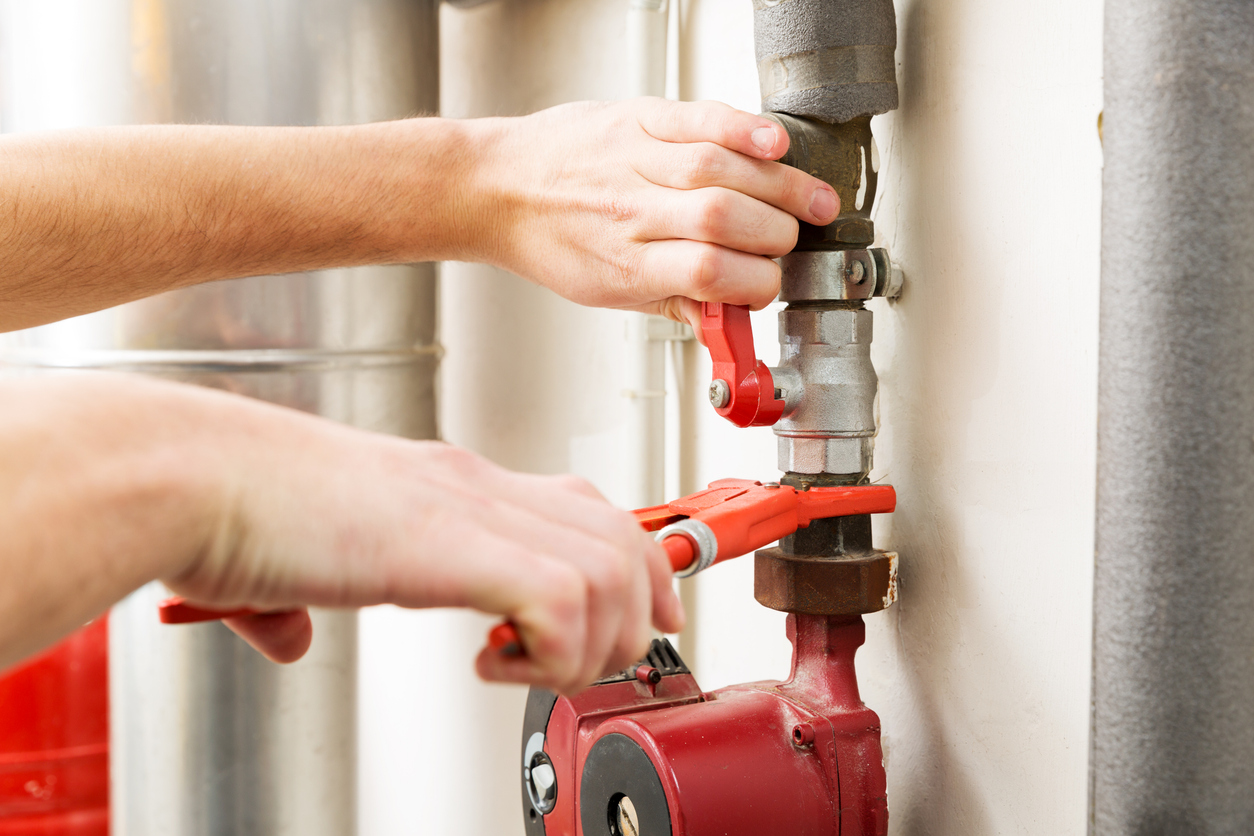
Which pumps are self-priming?
Self-priming pumps are of particular importance in numerous applications and industries. Their outstanding feature is that they are able to transport liquids from lower levels or containers without the need for prior filling or a permanent source of liquid. This makes them extremely versatile and useful in situations where conventional pumps cannot be used efficiently due to specific circumstances.
The advantage of self-suction capacity is particularly evident with positive displacement pumps. This type of pump produces printing and volume changes to move fluids. This creates a suction process which enables the pump to remove air or liquid from the suction area and provides a continuous flow rate to produce. Displacement pumps such as piston pumps, diaphragm pumps and peristaltic pumps are therefore often self-priming.
The connection types and hose options also contribute to self-suction capacity. For certain pump configurations, positioning the suction port or using special hoses can help optimize the self-suction process. Flexibility in hose selection and correct connection methods are crucial to ensure the effectiveness of self-suction.
How does a suction hose work in pumping systems?
The suction hose is an indispensable element for every pumping technology, as it is used to transport the pumped medium from the source to the pump. It connects to the pump via the suction port and thus enables the medium to be introduced. Made from flexible materials such as rubber or plastic, the hose ensures easy handling and secure sealing.
The unrestricted function of the suction hose is essential in order to flow rate not to interfere. Blockages could reduce pumping capacity. It is therefore important to regularly check and clean the hose to prevent contamination.
The placement of the hose also plays a role: Optimum positioning enables energy efficiency when introducing the medium. Regular inspection for damage is just as important. A damaged hose could lead to leaks and thus impair the pump function. In the event of damage, an immediate replacement should be carried out to ensure smooth pumping operation.
What does H Max mean in industrial pumps?
H Max stands for the maximum conveying height at industrial pumps. The delivery height is the maximum pressure that the pump can generate to transport liquids or gases. It is measured in meters or bar and indicates how high the pump can transport the medium in the line against gravity or resistance. Die rpm The pump significantly influences the Hmax value, as a higher speed usually results in an increased delivery height. The higher the Hmax value, the greater is the conveying capacity the pump. This value, together with the optimal speed, is particularly important when choosing the right pump for specific applications that require high flow rates, such as in the chemical industry or water treatment.
How does dry run protection work and what is it good for?
The Dry run protection prevents potentially harmful situations that could be caused by low fluid levels.
Using sensors or switches that monitor the liquid level, the dry-run protection detects when the level falls below a critical threshold. At this moment, the protective mechanism intervenes by deactivating the pump or putting it into a safe mode. This prevents the pump from continuing to work and thus sucking in air or running dry. Such a condition could cause significant damage to pump components, including overheating, wear, or blockages.
Particularly in industrial applications where large quantities of liquids are transported, the failure of a pump due to dry running can result in significant production downtime and financial losses. In private households or buildings where pumps are used for water supply or heating, dry-running protection is also of great importance in order to maintain the integrity of the pumps and prevent unwanted faults.
What connection types of industrial pumps are there?
Flange connection: This enables a secure connection between the pump and pipes, often used with larger pumps and higher pressures.
Threaded connection: Ideal for smaller pumps and low pressure applications due to their easy assembly and handling.
Clamp or quick release: This type of connection enables rapid assembly and disassembly of the pump, which is particularly advantageous during maintenance processes.
hose connection: Pumps that use flexible hoses may have special connections to securely secure the hoses.
Tri-clamp connection: Used in hygienic areas, such as food or pharmaceutical industries. Easy disassembly for cleaning purposes
Plug-in connections: Electric pumps use connectors for power supply and control.
Clamping ring connection: Specially used in chemical applications, it provides a reliable connection.